When the Eastern Australian Ground Control Group invited Principal, Penny Stewart to give a talk on machine learning applications in geotechnical engineering, Penny took the opportunity to demonstrate how machine learning AI enables fully automated ore fragmentation assessment. And, into the future could be developed to automate geotechnical inspections using 3d mapping data (digital surveying).
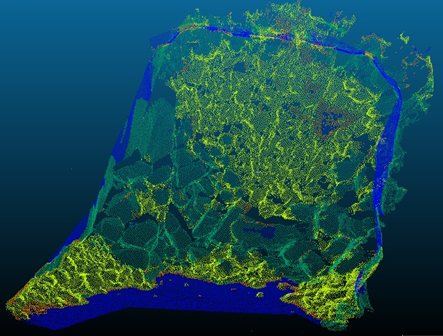
Our FRAGx algorithms uses 3D mapping point cloud data (e.g. UGPSRapidMapper, 3D Laser Mapping or MVS) to automatically assess ore fragmentation in less than a minute (Patent application no. 2017901586). The algorithms have been trained to automatically remove concrete floors and shotcrete from the assessment, and are unaffected by dark, wet, dusty and humid underground mine conditions. Until now, ore fragmentation assessment required an hour of manual processing, off-site processing, and/or very high lighting.
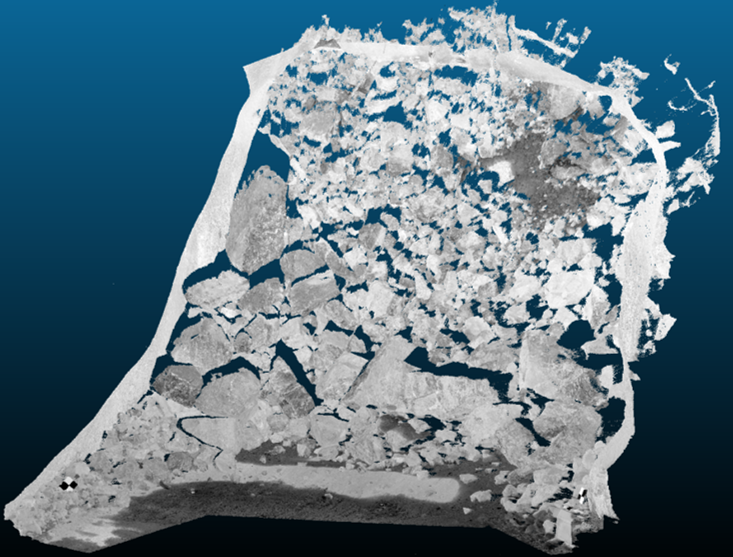
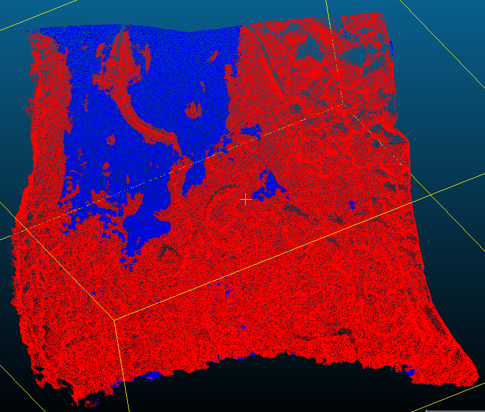
What’s next?
These algorithms can also be trained to carry out geotechnical inspections using 3d mapping data (digital mine surveys). For example, we expect to be able to train these algorithms to recognise:
- Spalling
- Cracked shotcrete
- Plate deformation, missing plates and mesh bagging.
Whilst these algorithms won’t be as accurate as a professionally trained geotechnical engineers, they have the potential to cover large areas quickly as part of digital mine surveys (using 3d mapping).
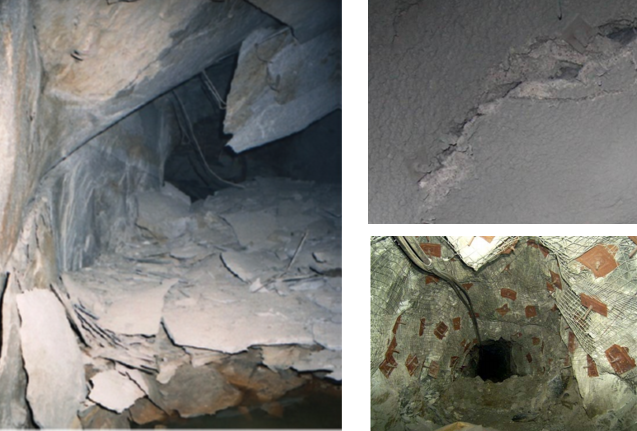
For those not familiar with the 3d mapping technology, this YouTube video shows lidar scanning in action. Whilst uGPS Rapid Mapper lidar data can be processed on site as part of Deswick mining software, and ZEB data can be processed on-site using a range of software, the MVS system and some 3d Laser Mapping solutions are offered as off-site processing services.
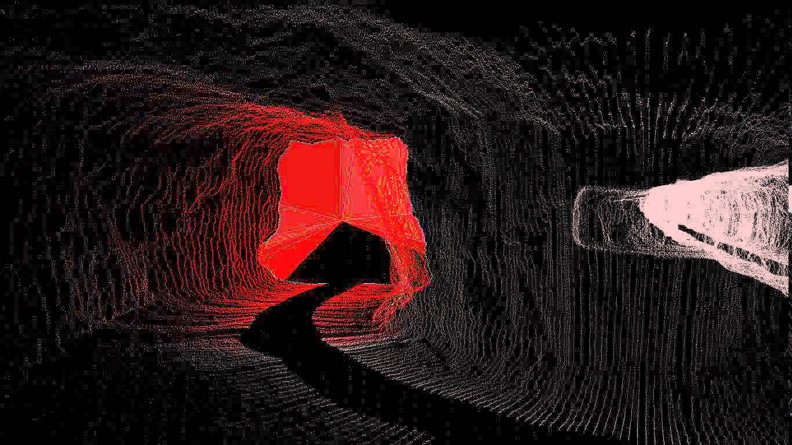
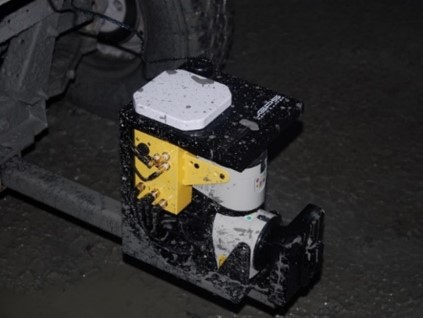
Together, 3d mapping and machine learning AI offers an array of exciting opportunities for geotechnical engineering, not just for underground, but also for open pit wall inspections/assessment. We look forward to bringing our algorithms to these very exciting developments!