The Problem:
A large copper-gold porphyry operation in Western Australia saw the potential in automated process decision support for improved and consistent process performance.
The site requested assistance with the selection of set points or process levers for the optimum and consistent plant performance. The operating strategy at this site was based on the experience and intuition of operators and metallurgists and their interpretation of process conditions that lead to best performance.
Sometimes the approach is systematic and changes are made in a stepwise measured way. Other times the approach is erratic with large and frequent changes leading to reagent overdosing, process instability and large circulating loads. All of which deliver poor process performance and ultimately low metal recovery.
The Solution:
To better support operators and plant metallurgists in processing plant set point decisions, MAXTAProcess was implemented in the flotation circuit of a large open pit copper-gold porphyry operation to recommend reagent addition rates and mass pull rates to maintain low copper tail grade and thereby maximise copper recovery.
Using about 2 years worth of operating data and information accessible via the data historian, OSIsoft’s PI. MAXTAProcess was able to build a digital twin of the operation incorporating the whole value chain from the geological block model to the flotation circuit. This was possible as the fleet management data containing geological properties of the ore is also captured in PI at this site, meaning tracking of ore from the geological block model through to the plant was not required.
The first part of the approach for this process plant application was the development of a machine learning prediction model that would forecast flotation Cu tail grade ahead of time provided the plant was running in steady state and excluding any process excursions such as manual reduction in feed rate because of outside issues.
The flotation Cu tail grade was predicted 6 hours in advance even though the flotation circuit residence time is less than 30 minutes. The machine learning prediction model was heavily dependent on the geological properties of the ore, as well as the performance of the plant (crushing and grinding circuits) upstream of the flotation circuit. Recommended operational set points were matched to the properties of the ore the conditions in the plant upstream.
In order to recommend flotation set points for best flotation performance, conventional mathematical optimisation technique was overlayed on the machine learning prediction model. An historical view of the operating strategies suggests optimum process plant set points for best plant performance when treating similar ore properties in the past.
MAXTAProcess set points are recommended every 6 hours to limit frequent and large changes in process set points which commonly lead to circuit instability.
MAXTAProcess has the ability to manage data quality issues in near realtime. Through the use automated algorithms for sensor health and instrument calibration. This ensures process predictions and setpoint recommendations are true and accurate.
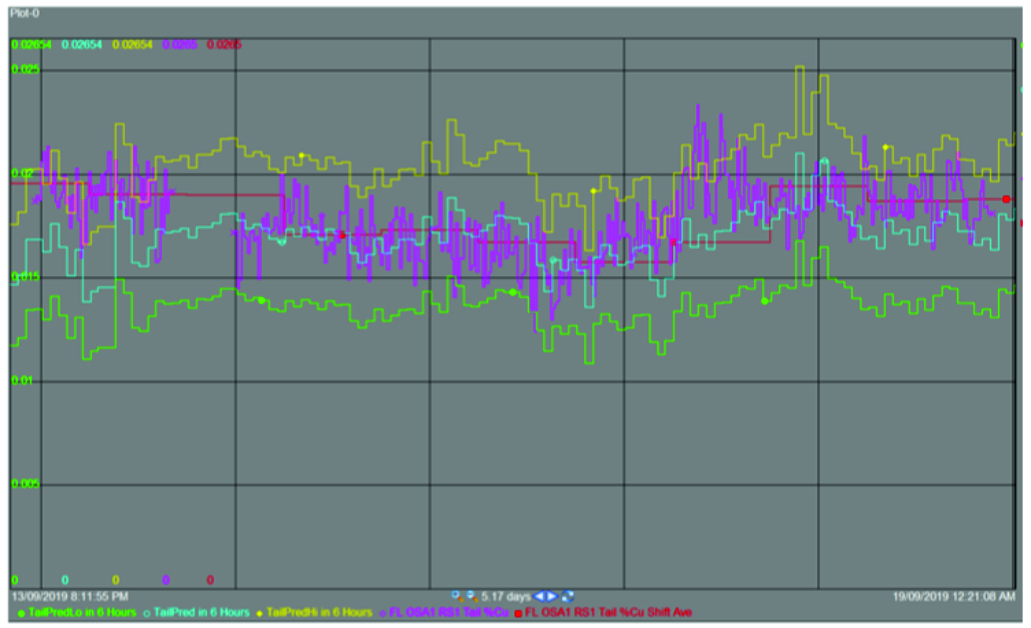
In this instance, MAXTAProcess is deployed seamlessly within the OSISoft PI framework via a secure App where MAXTAProcess set point recommendations are reported as additional tags within the control system.
The implementation and deployment of MAXTAProcess involved close collaboration with the site process control team as well as the site metallurgists. It was conducted over a period of 12 weeks from the receipt of operating data to the deployment of MAXTAProcess.
The Results:
MAXTAProcess provided real time operator decision support via the operating and control system, PI by OSIsoft. MAXTAProcess offered set point recommendations to the operating strategy for improved operating stability and optimised plant performance.
Simulated results show MAXTAProcess set point recommendations can act to simultaneously achieve flotation copper tail grade below 0.02%Cu and reduce the overall copper tail grade by about 0.0013%Cu, resulting in up to 1.5% increase in copper recovery.
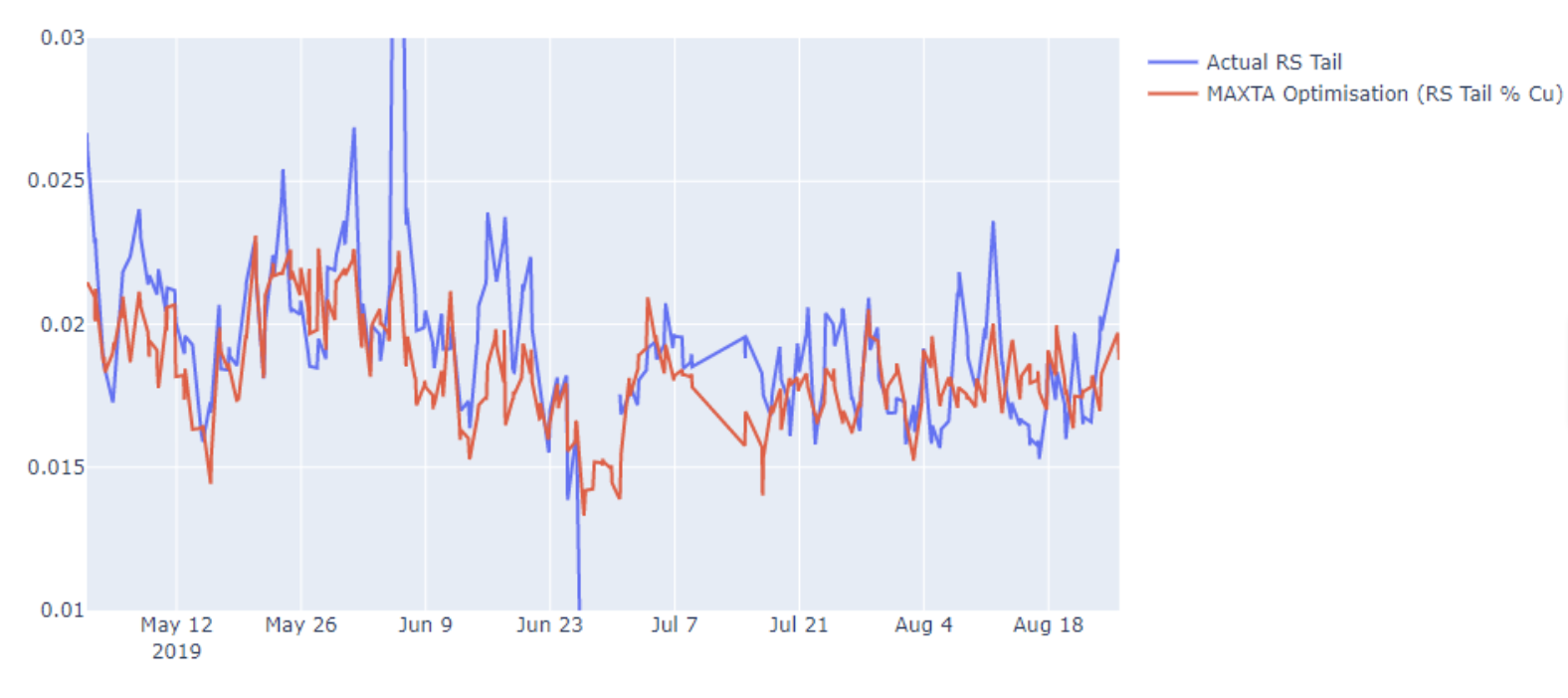
MAXTA is available now for demonstration, please contact us to arrange a walk through.