This article was first published by Mining Magazine, 3 June 2017 and is reproduced here with permission of the writer and editor, Carly Leonida. I would also like to take this opportunity to acknowledge that these algorithms wouldn’t be operational, if it wasn’t for Newcrest’s world class achievement in partnering with a start-up to take a prototype solution (from Brisbane 2016 Unearthed Hackathon) into operations so quickly! Also a few pics have been added that don’t appear in the full article:
Dr Penny Stewart, managing director and principal at PETRA Data Science, is a busy person. Nonetheless, in early May, between preparing her presentation for the upcoming Austmine 2017 conference, which will take place in Perth in late May, and catching a flight, she found a few minutes to speak to me from an airport departure lounge.
And the reason for our call? At the start of the year, the company achieved something rather special, perhaps even a world-first in mining: it has enabled Newcrest Mining’s Lihir operation to avoid overload events in its semi-autogenous grinding (SAG) mills (read: unplanned downtime) with the help of machine learning algorithms; something you, our readers, will want to know about.
Located on Aniolam Island in the New Ireland Province of Papua New Guinea, the gold deposit at Lihir is one of the largest in the world; since starting production in 1997, the mine has produced more than 10Moz of gold. Most of the ore is refractory and is treated using pressure oxidation before the gold is recovered by a conventional leach process.
Stewart explained to me how the project came about. “We had worked together before, although this was our first project with the digital team,” she said.
“We took part in the Unearthed Hackathon in Brisbane [Australia] in March 2016. The team from Newcrest was there. They saw what we were doing and arranged for us to talk to the reliability team at Cadia East, and that led to us working with them to minimise pump downtime at the operation.”
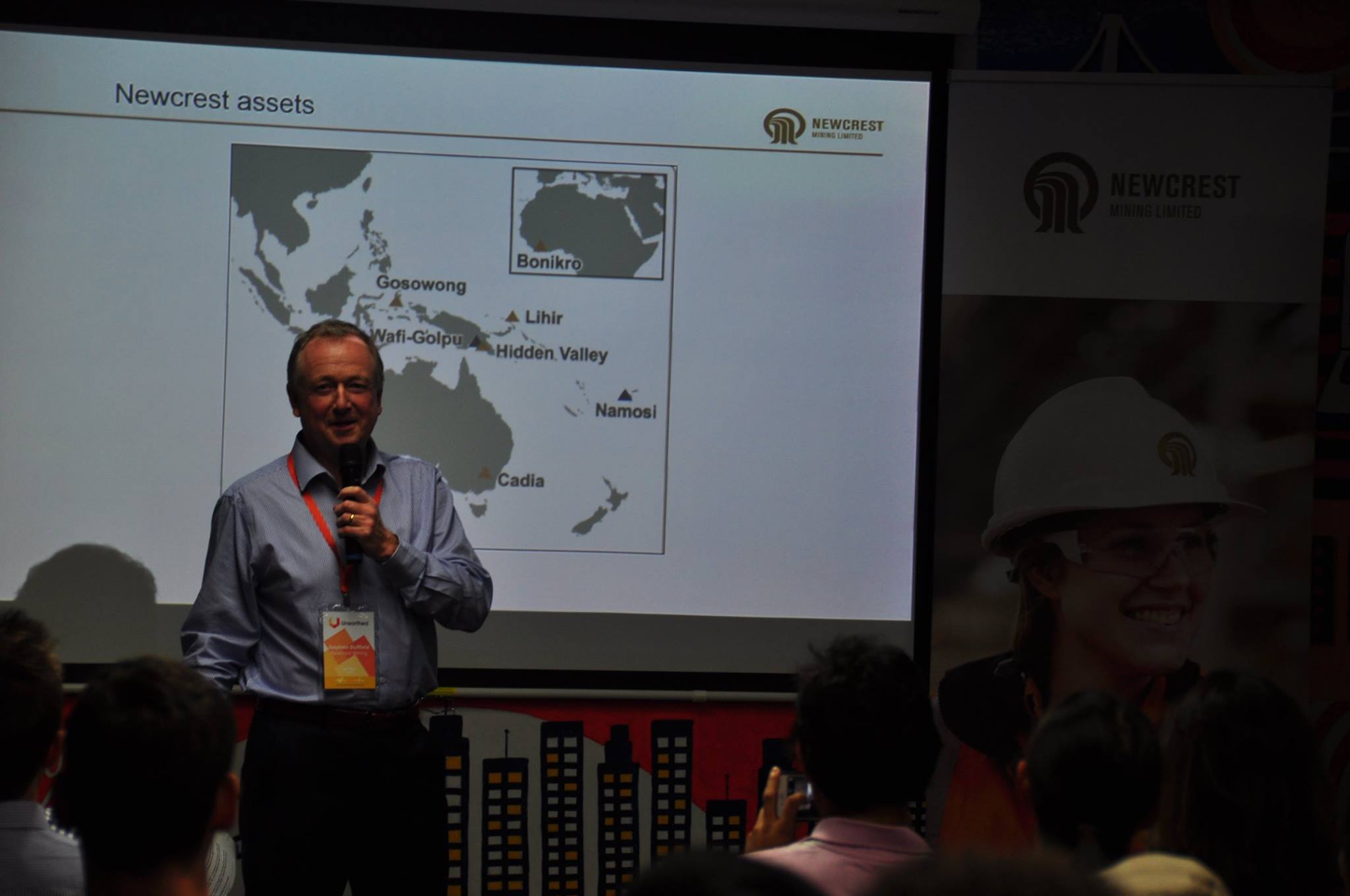
This led to further work at Lihir. The mine operates three SAG mills and, in October 2016, Newcrest engaged PETRA to develop overload algorithms for each of the machines.
“When a SAG mill overloads and becomes too full, it causes the mill to trip and stop,” Stewart explained.
“Sometimes it can take quite a while to get it running again. Because the SAG mills at Lihir are critical pieces of production equipment, and there’s no way of diverting material, it was really important to avoid these events wherever possible.”
Indeed, every minute of downtime equals lost production, and the power draw (and cost) required to restart a SAG mill is significant.
Stewart talked us through the algorithm development process. “We take historical data going back a year or two, in this case it was one year, and we look at the critical signals or indicators related to overload events,” she said.
“There is a huge amount of data that comes off a SAG mill – noise is recorded, power, speed, energy consumption and control parameters – there are hundreds of measurements, usually taken at five-second intervals that need to be analysed.
“We take all of that data and use the patterns and anomalies to predict what’s going to happen next. There are leading indicators as to what’s going to happen, and an algorithm is a mathematical equation that describes all of those signals. It either feeds that information back into the mine’s automated process control system or, in this case, it triggers a visual warning so that the operators can respond to the increasing probability of an overload event. At Lihir, the algorithm predicts the probability of an overload event in an hour’s time, which allows the mine to take appropriate action to prevent it.”
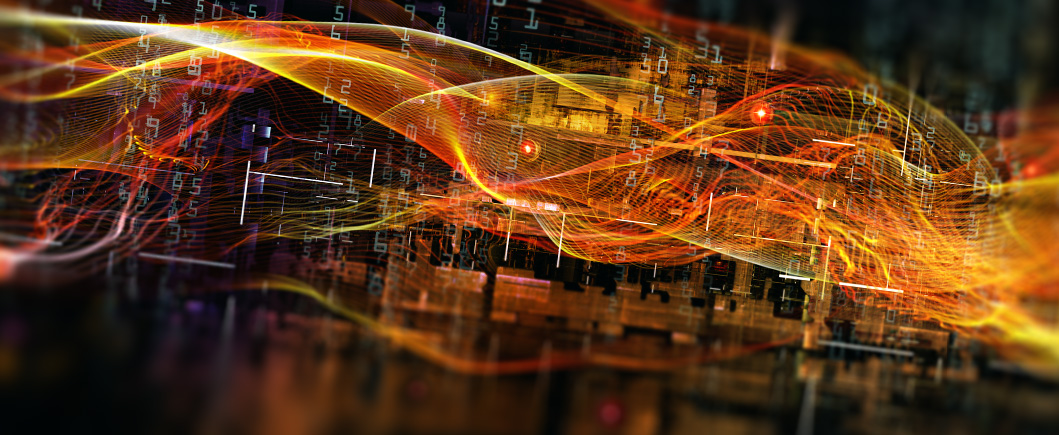
Lihir has different levels of response that it deploys depending on the likelihood of an event occurring, and each of the three mills has its own algorithm. “For each one, there weren’t many overload events recorded compared with normal operating data,” Stewart explained, “so it was difficult to identify that tipping point from normal operating conditions into an overload situation.
“The algorithms effectively allow the mills to operate at maximum throughput with minimum risk of overload. The main challenge was the quantity of data based on failures compared to normal operating conditions, which made it difficult to predict when these events were going to happen, particularly an hour in advance.
“Often, machine learning specialists use unsupervised machine learning in this type of scenario, but in this case, that wouldn’t give the mine enough time to respond. That’s the advantage of using a supervised machine learning algorithm.”
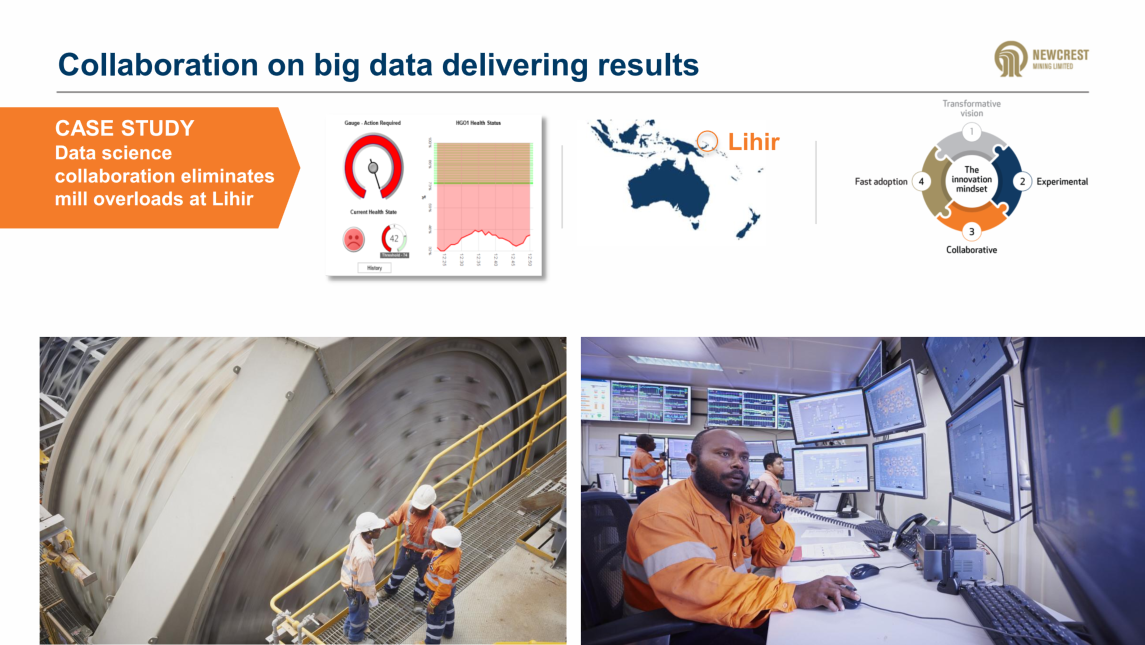
So what benefits has the project delivered? Stewart is rather modest: “Obviously I can’t give exact figures relating to this case, but I can say that preventing one or two downtimes paid off the cost of the project,” she said. “Lihir was having multiple overload events each year. And since implementing the algorithms in January this year, they haven’t experienced any overloads.”
This success has led to further collaboration between the two companies. “We have created other algorithms for Newcrest as well, and we’re also working on their big data mine-to-mill studies,” Stewart added.
“From what I can tell this hasn’t really been done before; using live algorithms to predict downtime events in hard-rock mining. The same sorts of algorithms are being used in oil and gas, and we’re just about to partner with Woodside [an Australian oil and gas producer] on a similar project. That’s a big win for us.”
She continued: “Newcrest is one of the first in the world to implement live algorithms to prevent downtime, but as word gets out, I expect interest from the mining community will grow. After all, this is something that can be done on existing systems; you don’t need to spend money on a new platform to deploy these algorithms, they’re platform agnostic.
“Hopefully, at the Austmine event, more people will come up and talk to us.”
With that, Stewart heads off to catch her plane. And just a few days later, PETRA’s FORESTALL® downtime prediction algorithms were named as a finalist in the Austmine 2017 Awards METS Innovation category.
It seems Stewart is right; the company is on to something big here!